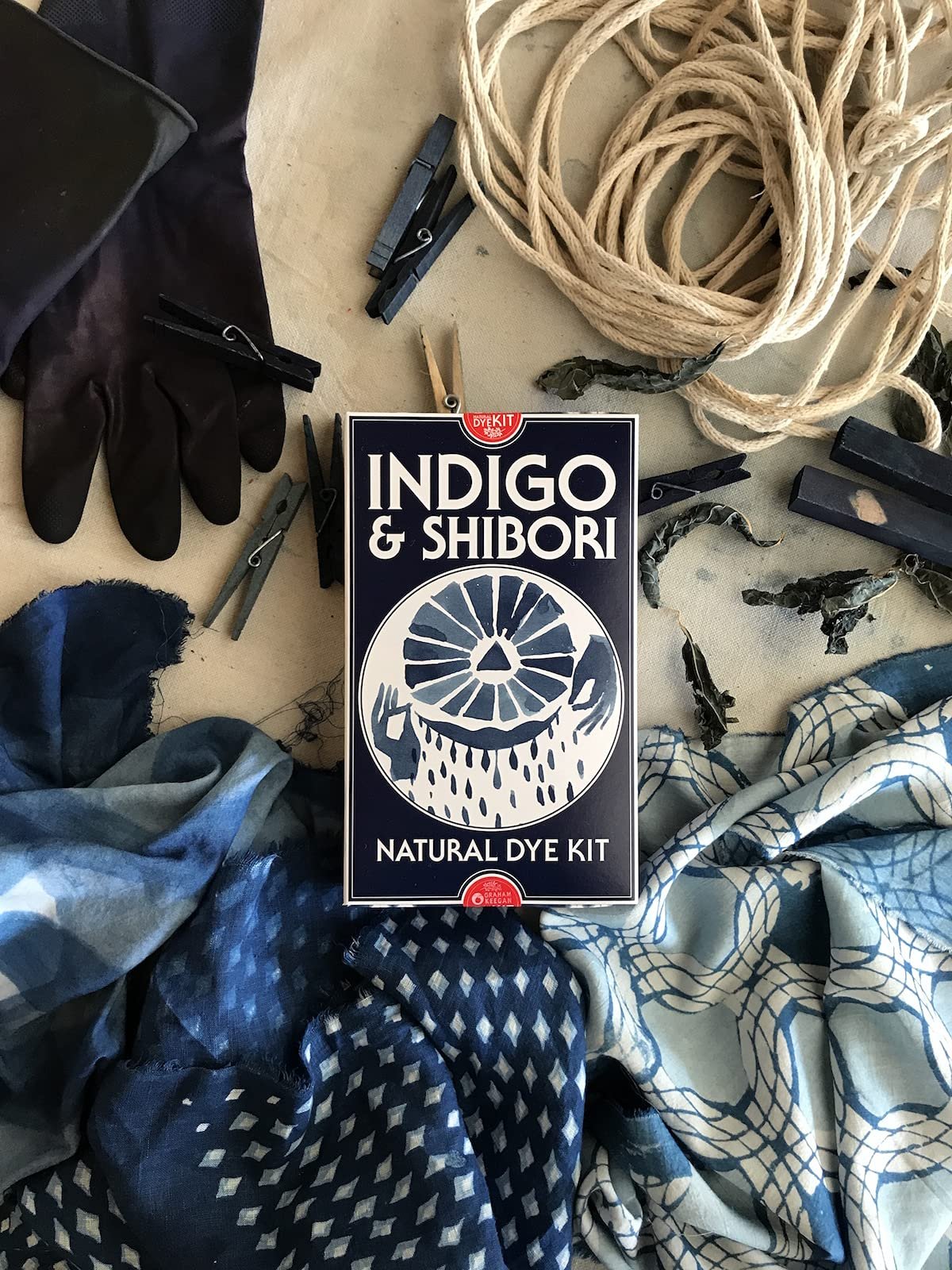
INDIGO DYEING : Questions & Answers
Some of the questions on this page are specific to indigo dyeing using our Indigo & Shibori Natural Dye Kit, but many are applicable to indigo dyeing more broadly!
Your dye kit comes complete with a load of supplies and materials that you can use to make designs on fabrics. Some parts of the process are complex and we may not have had room in the printed instructions included to go in depth.
If you have a question that has not yet been answered to your satisfaction, ask away!
USE KEYWORDS TO SEARCH FOR ANSWERS TO YOUR QUESTIONS
The following is an index list of each Question and Answer title, click on the title to read the corresponding Q&A, or simply use search terms in the search box above to see if your question has been answered!
-
DIP TECHNIQUE
- Jul 26, 2023 Avoiding Fading
- Jul 26, 2023 Dipping Resist Pieces
- Jul 26, 2023 Maintaining Your Whites While Rinsing
- Jul 25, 2023 Dyeing Over Multiple Days
- Jul 25, 2023 Avoiding Sediment
- Jul 25, 2023 How Sediment Affects Your Dyeing and the Importance of Proper Rinsing
- Jul 25, 2023 Tips for Using Rice Paste in a Ferrous Vat
- Jul 25, 2023 Tips for Getting the Darkest Blues
- Jul 25, 2023 Suggestions for Uneven Coloration
- Jul 25, 2023 Rinsing Stencil Print Between Dips
- Jul 25, 2023 Number of Dips for Different Shades of Indigo
- Jul 20, 2023 Avoiding Sediment in the Ferrous Indigo Vat
-
DYE GARDEN QUESTIONS
- Jul 26, 2023 Starting Indigo Seeds Indoors Versus Outdoors
- Jul 25, 2023 When to Plant Indigo Seeds
- Jul 25, 2023 Indigo Seed Propagation
-
GENERAL INDIGO DYEING QUESTIONS
- Jul 26, 2023 Calculating Amount of Indigo Needed
- Jul 25, 2023 Dyeing Protein Fibers in a Natural Indigo Vat
- Jul 25, 2023 Dyeing Stretch Fabric with Natural Indigo
- Jul 25, 2023 Ferrous Vat Longevity
- Jul 25, 2023 Shelf Life of Natural Indigo and “Pasting-Up” Your Powder
- Jul 25, 2023 Toxicity of Indigo and Indigo Dyeing
- Jul 25, 2023 Indigo and Splatter Dyeing
- Jul 25, 2023 Indigo and Cotton Velveteen
- Jul 25, 2023 Indigo and Polyester
- Jul 25, 2023 Over-dyeing with Indigo
- Jul 25, 2023 Is Indigo Dye Okay for Sensitive Skin, Is it Safe Enough to use on Baby Clothes?
- Jul 25, 2023 Light and Pale Shades of Indigo
- Jul 25, 2023 Fixing Indigo Onto Fabric
- Jul 25, 2023 Materials and Fabrics Suitable for Indigo Dyeing
- Jul 25, 2023 Disposing of a Ferrous Indigo Vat
- Jul 25, 2023 Large Container e.g. Trash Can Vat
- Jul 20, 2023 Dye Vat Capacity
-
INDIGO LEAF EXTRACTION
- Jul 25, 2023 Making a Ferrous Vat with Fresh Indigo Leaves
- Jul 25, 2023 Clarification on Indigo Extraction
-
INDIGO VAT TIPS & TROUBLESHOOTING
- Jul 26, 2023 Is the Fermentation Vat the Best Vat?
- Jul 26, 2023 Indigo Vat Troubleshooting: No Longer an Odor
- Jul 26, 2023 Indigo Vat Troubleshooting: Dark Blue Vat
- Jul 26, 2023 Indigo Vat Troubleshooting: Greenish Tint
- Jul 26, 2023 Avoiding Fading
- Jul 26, 2023 Waiting 24 Hours Between Mixing and Using Your Indigo Vat
- Jul 26, 2023 Quantity of Indigo Paste in a Vat
- Jul 26, 2023 Making a Long Term Vat
- Jul 25, 2023 Indigo Flower Comes and Goes
- Jul 25, 2023 Using Pencil to Make Marks on Fabric - Does Graphite Affect the Vat?
- Jul 25, 2023 Under-Reduced Fructose Vat
- Jul 25, 2023 Troubleshooting a Different Vat Recipe
- Jul 25, 2023 Avoiding Sediment
- Jul 25, 2023 Indigo Vat Troubleshooting: Recipe Quantities for a Large Vat
- Jul 25, 2023 Sharpening Your Vat
- Jul 25, 2023 Stirring Your Vat
- Jul 25, 2023 Adding More Pigment to a Fresh Leaf Extraction Vat
- Jul 25, 2023 Making a Vat for Pale Dyeing
- Jul 25, 2023 Sizing Up Your Vat
- Jul 25, 2023 Indigo Vat Troubleshooting: Lye and Hydrosulfite
- Jul 25, 2023 Recipe for Pickling Lime and Fructose Vat
- Jul 25, 2023 Thoughts on Using Soda Ash and Spectralite Instead of Iron and Lime in Making a Dye Vat
- Jul 25, 2023 Giving Your Vat Enough Time to Set Up
- Jul 25, 2023 Switching Reducing Agent and pH Combo When Sharpening Your Vat
- Jul 25, 2023 Vat Temperature
- Jul 25, 2023 Precision of pH for Ferrous and Fructose Vats and Indicators of Under or Over Reduction
- Jul 25, 2023 Forms of Indigo that Work in a Ferrous Vat Recipe
- Jul 25, 2023 Indigo Vat Troubleshooting: Sludge and Sediment
- Jul 25, 2023 Indigo Vat Diagnosis: Vat Color, Flower, and pH
- Jul 25, 2023 Iron Vat Temperature
- Jul 25, 2023 Dissolving Lime in an Indigo Vat
- Jul 25, 2023 Reviving a spoiled or 'oxidized' indigo dye vat
- Jul 25, 2023 Mixing and Combining New Vat Ingredients with Old or Spent Vats
- Jul 25, 2023 Indigo Vat Mixing Temperature
- Jul 25, 2023 Weak Vat, Old Vat and Vat Health Restoration
-
PRE AND POST-DYE TREATMENTS & TIPS
- Jul 26, 2023 Preventing Crocking and Dyeing Large Fabrics Like Bedding
- Jul 26, 2023 Avoiding Fading
- Jul 26, 2023 Rinsing in Still Versus Running Water
- Jul 25, 2023 How Sediment Affects Your Dyeing and the Importance of Proper Rinsing
- Jul 25, 2023 Troubleshooting Strange Fading Patterns and Discoloration
- Jul 25, 2023 Suggestions for Uneven Coloration
- Jul 25, 2023 Fabric Drying Stiff and Crispy Post-Dyeing
- Jul 25, 2023 Indigo Post-Dye Rinse: Purposes and Options
- Jul 25, 2023 Protecting Your Indigo-Dyed Pieces From Fading: Proper Scouring and Soy Milk Treatment
- Jul 25, 2023 Sun Fading of Indigo
- Jul 20, 2023 Best Way to Dry Indigo Dye
-
QUESTIONS ABOUT OUR INDIGO & SHIBORI DYE KIT
- Jul 26, 2023 Waiting 24 Hours Between Mixing and Using Your Indigo Vat
- Jul 25, 2023 Scaling Down Vat Size
- Jul 25, 2023 How Much Fabric Will the Natural Indigo & Shibori Dye Kit Dye?
- Jul 25, 2023 Ferrous Vat Longevity
- Jul 25, 2023 Components in the Natural Indigo & Shibori Dye Kit
- Jul 25, 2023 Indigo Form in the Natural Dye Kit
- Jul 25, 2023 Indigo Kit and Dyeing Large Items
- Jul 25, 2023 Light and Pale Shades of Indigo
- Jul 25, 2023 Scent of Natural Indigo
- Jul 20, 2023 Dye Vat Capacity
-
RICE PASTE
- Jul 26, 2023 Dipping Resist Pieces
- Jul 26, 2023 Pastry Cones for Applying Rice Paste Resist
- Jul 26, 2023 Indigo Resist Screen Printing
- Jul 26, 2023 Rice Paste Resist Longevity
- Jul 26, 2023 Destabilized AKA De-Fatted Bran in Rice Paste Resist
- Jul 25, 2023 Tips for Using Rice Paste in a Ferrous Vat
- Jul 25, 2023 Rinsing Stencil Print Between Dips
-
TIPS FOR VARIOUS DYE PROJECTS
- Jul 26, 2023 Preventing Crocking and Dyeing Large Fabrics Like Bedding
- Jul 26, 2023 Using Fresh Goldenrod Leaves to Make a Paintable Dye Pigment
- Jul 26, 2023 Type of Wood for Making Block Prints
- Jul 26, 2023 Mordant Recipe: Block vs Screen Printing
- Jul 26, 2023 Making a Stamp Pad
- Jul 26, 2023 Dyeing with Fresh Plants
- Jul 26, 2023 Indigo Resist Screen Printing
- Jul 26, 2023 Destabilized AKA De-Fatted Bran in Rice Paste Resist
- Jul 25, 2023 Dipping Metal in my Vat
- Jul 25, 2023 Using Natural Indigo Paste
- Jul 25, 2023 Dyeing Vegetable Tanned Leather
- Jul 25, 2023 Tips for Using Rice Paste in a Ferrous Vat
- Jul 25, 2023 Dyeing Paper
- Jul 25, 2023 Chalk and Cheesecloth Clarification in Mordant and Block Printing
-
USING MORDANTS
- Jul 26, 2023 Mixing Mordant
- Jul 26, 2023 Mordant Recipe: Block vs Screen Printing
- Jul 26, 2023 Diluting Mordant Paste
- Jul 25, 2023 Chalk and Cheesecloth Clarification in Mordant and Block Printing
Is the Fermentation Vat the Best Vat?
Q: Is the Fermentation Vat the Best Vat?
A: This is an ongoing, developing manifesto on a pro-fermentation position - Last Updated September 20, 2022
Short answer, yes. The fermentation vat is the best vat that I’ve worked with.
If you’re new to the realm of indigo vats there’s some basic terminology to get under your belt. First is the term “vat”. It refers to a liquid solution which contains water, indigo pigment, something alkali and some sort of reducing agent which activates the indigo - allowing it to dye onto fabrics. Vats are typically described by the reducing agent which has been used - e.g. fructose vat (some sort of fruit sugars, whether gleaned from fruit pulp or purchased powder), ferrous vat (powered by iron), zinc-lime vat (you get it - powered by zinc and lime), thiox vat, etc. These vats are all of a type which are powered by their ingredients - if it stops working, you can simply add more of the ingredients (to a point), and things will get going again. I think of all these vats as ‘recipe’ vats - add some this, add some that and boom, you’re dyeing.
Over the past couple years, I’ve been working with fermentation vats - I think of these more as ‘relationship’ vats. I find the process similar to making and monitoring a sourdough starter, vinegar making from fruits or making kimchi or sauerkraut. Yes, there is an initial combination of the necessary ingredients, but following that combination - there is a daily practice - a relationship with the vat that develops where you can read the conditions of the vat and make appropriate decisions about how to keep it healthy.
I’m finding the distinction between ‘recipe’ and ‘relationship‘ to be essential.
The purpose of pursuing a natural dye practice is to engage more fully with the world around us. Over time, I’ve become more and more troubled by the popular, published approach to ‘natural’ dyeing and its reliance on a commercial/industrial apparatus to supply the materials and ingredients necessary. It has gnawed at me for years - my own lack of understanding of materials used in ‘natural’ dyeing. I believe myself to be quite informed on materials and processes - yet I found that so many of the ingredients called for in ‘natural’ dye are products of an industrial apparatus that I had close to zero understanding of their production and sources. Do you know what Slaked Lime is? Have you seen how it is produced? How about Alum? Ferrous sulfate? Any ‘natural’ dye extracts? Can you prove that those are actually what they say they are? Would you ever bother to do so? What portion of your dye ingredients do you know how to create? How much of your process is reliant on a system that you cannot see the workings of? How far away did these ingredients come from to reach you? Does it have to be like this?
I don’t think that natural dyeing is a solution to any ills of our contemporary industrial textile dyeing apparatus. Natural dye processes are traditionally very resource intensive - involving heavy water use as well as lots of combustion of hydrocarbons to heat liquids. I cannot conceive of a sustainable scale of production that would keep pace with the demands of the people - without being deleterious to the shared environment. I’d like to acknowledge natural dyeing’s actual current role in the ‘developed’ world. I believe the practice exists as a existential relief - an anathema to industrial systems.
The same yank - need to have control leads us to want to use crazy colors - and so requires the use of foreign extracts, extreme choices - rare foreign bugs, collected and shipped from thousands of miles away. Just admit - you may live in a boring place or way.
Preventing Crocking and Dyeing Large Fabrics Like Bedding
Q: How do I prevent indigo dye from rubbing off onto other surfaces when the fabric is subjected to abrasion? My daughter dyed some bedding with a very similar kit and over time it left blue in our dryer and stained some other bedding/clothing.
A: Great question! Also, the tendency of a dyed fabric to give off color when the surface is rubbed is called crocking. Bedding is notoriously challenging to dye well in home use kits! Every sheet or duvet cover or whatever is just so much material that it often overwhelms the activity of the vat and causes the vat chemistry to become oxidized and the indigo becomes under-reduced which causes poor color uptake into the fabric. This leads to more crocking of your goods.
Also, large items will inevitably stir up whatever sediment exists at the bottom of the vat which can also 'clog' (for lack of a better term) the fabric which will also lead to poor and uneven color uptake.
I mostly dye indigo in a 50 gallon vat - and that can handle sheets and larger yardage panels but even I don't dye them often! Sheets are a great place to practice some larger folded patterns though. And they're much easier to dye when folded into bundles. I recommend keeping the total number of layers of the material under 25 otherwise you just end up with a LOT of white area.
My recommendation for optimizing color uptake on large items and avoiding crocking would be to pre-soak the goods in hot water prior to going in the vat with the addition of a little soda ash - say a tablespoon per gallon. This alkaline water can really help wet out the fabric and will help keep the pH of the vat from shifting toward acidic.
Other than that, rinse rinse rinse prior to washing after dyeing. And I always wash indigo goods alone on their first laundering. Also I never wash in a front loading washer with the tight seals. Those can actually create and maintain a reduction environment which can discharge some color from the piece during the cycle. I wash all my indigo goods in a top loader on the gentle setting with detergent.
There are also soy coatings made from fresh bean soy milk that can be added onto fabric after dyeing to essentially seal in the indigo but those require ageing and oxidizing (for at least a few weeks) before washing. They act as a transparent protective later. I hope to post more about that soon. John Marshall covers that process in his book Singing the Blues - shameless plug - which is available on my website www.grahamkeegan.com
Using Fresh Goldenrod Leaves to Make a Paintable Dye Pigment
Q: How can I make a paintable dye pigment from goldenrod leaves?
A: You will want to fill a pot with your fresh goldenrod leaves and top it up with water. Boil the water and leaves for about an hour. Then remove the leaves and boil off the excess liquid until the remaining concentrate is a syrupy consistency. From there, add in a pinch of cream of tartar and equal parts by volume of an alum mordant (100g vinegar, 20g alum sulfate, 10g soda ash, 1g guar). This mixture can be applied by brush or stencil. Rinse and fix after drying.
Mixing Mordant
Q: I am using your mordant recipe and I am curious how long I need to blend all of the ingredients.
A: When mixing up mordant, the iron and alum need the most mixing. They will both dissolve fully and there will be no particulate or sediment when they are fully blended. The lime, probably 30 seconds or so, and the guar, just mix until the medium stops getting any thicker.
Type of Wood for Making Block Prints
Q: What kind of wood do you use for making block printing blocks?
A: The wood I usually use is balsa because it is so easy to carve. It isn't that strong and will break down about as quickly as foam would. You can use any kind of wood for carving, though make sure that you're carving into the end grain.
Mordant Recipe: Block vs Screen Printing
Q: Is the mordant recipe the same for screen printing as it is for block dyeing?
A: When screen printing with dyes I use the exact same mordant recipe that I use for block printing. If you want, you can thicken the print medium a little more to get it to behave better on the screen by adding about 50% more guar gum (the thickener).
Indigo Vat Troubleshooting: No Longer an Odor
Q: My vat smelled really pungent when I first made it but now the smell is gone. Did something go wrong?
A: My guess is that all the active ingredients have probably settled to the bottom, try re-heating and sharpening if need be and see what happens!
Indigo Vat Troubleshooting: Dark Blue Vat
Q: My vat is dark blue and not dyeing correctly, any idea what is wrong?
A: If your vat is dark blue, it is under-reduced. Are you using a metal container? If you heat the vat up to 120F (or higher) you can force out some of the dissolved oxygen, and it should redevelop the coppery scum on top. Stir it, let the sediment settle out for at least a half hour, then do another round of dyeing. You can also follow my directions on sharpening on my website : http://www.grahamkeegan.com/indigo-vat-basics/
Indigo Vat Troubleshooting: Greenish Tint
Q: My vat has a greenish tint to it, is something wrong?
A: The vat should always have a greenish tint, though the oxidized indigo on your fabric should always appear blue. If there is a greenish tint there, you hit the sediment when you were dipping and your piece has got iron crud on it. You can wash with citric acid and soap alternatively until the piece goes back to pure blue. Avoid the sediment, but if you do get some on your piece, rinse it off immediately and THOROUGHLY.
Calculating Amount of Indigo Needed
Q: Is there a way to calculate the quantity (weight) of fiber I'm gonna be able to dye with a given quantity of indigo?
A: Potentially... There are so many factors though including the fiber type, weave or knit structure, fiber weight, concentration of the indigo pigment, reduction type and reduction state, depth of shade and amount of coverage.
I think it would be more of a thing where you dye some fabric just the way you like it and then develop a recipe based on first results. It would be challenging to be predictive about it...
Making a Stamp Pad
Q: I would like to try printing with blocks. Any tips on making a stamp pad?
A: I use a plywood block as the base and then set a thin (1/8-1/4") sponge on top of it, trimmed to fit exactly. Then I wrap that whole business in 60 or 80 mesh screen. It gives a much more even distribution of the print medium than cheesecloth.
Dyeing with Fresh Plants
Q: Any general tips for dyeing with actual fresh plants?
A: I've found it is best to work with simmering liquids, no need for vigorous boils. If its a leafy green plant, I'll heat the liquid first then add the greens and simmer for 20 minutes at least. Woody or root-y things, I'll simmer for an hour, then remove the dyestuff, keep the pots hot, but on low heat and make sure to keep agitating the fabric goods.
Avoiding Fading
Q: I dyed several pieces in a ferrous vat and had great results. They came out with great deep blues. However, they have faded terribly since then. Any idea what I might be doing wrong?
A: The typical culprits on fading are:
Choice of material being dyed. Some materials have received inadequate preparation and have some sort of coating remaining on the fiber itself which keeps the indigo from dyeing directly to the cellulose. Well scoured materials will dye more evenly and will hold up to all kinds of wear (UV, Washing). Some fibers also just dye more easily. For example rayon is super easy to dye and linen is more challenging.
Conditions in the vat may have been under-reduced, meaning that the indigo was not in proper shape to adhere to the fabric.
Sediment layering. If your fabric hits the sediment on an early dip, future dips will adhere to the gunk layer you picked up from the sediment and then wash out later as the sediment itself eventually breaks down and moves along.
Dipping Resist Pieces
Q: Any best practices for dipping pieces with resist patterns on them?
A: Yes, here are a few:
Be very careful when dyeing and removing your pieces from the vat as any drips will begin to weaken the vat. Remove your pieces very slowly and that will minimize.
Make sure you soak your goods in cold water with a drop or two of synthropol (which helps with dye penetration) so they are nice and saturated before they go in the vat. This will allow for even dye uptake.
If you are using wax resist make sure your vat is cool enough so the wax won’t melt when you dip.
Make your vat in as tall and skinny of a container as possible so you can fully submerge your piece without it getting in the sediment.
Set your pieces onto little wire rings that fit inside your container. (i just make mine with moldable wire from the hardware store, often used for clothesline) and dip them so they never touch themselves. Always fully wet your waxed pieces in cold water with a drop or two of synthropol (which helps with dye penetration) prior to their entry into the vat. Here's a video of an impromptu ring that I made. https://www.instagram.com/p/BKq390-DAC1/?taken-by=yesgraham
Diluting Mordant Paste
Q: I’ve been experimenting with the iron and alum pastes and I have some questions. I printed on scoured cotton canvas and dyed in a light cochineal. My print came out looking like the iron paste barely changed colors. Any idea why this happened?
A: I've never used Cochineal so I can't speak to that specifically, but generally, when I'm using a weak bath of dye, I'll use a diluted mordant. So, the recipe that I posted on the site is for a FULL STRENGTH mordant paste. You can dilute that by up to 10x at least (just use 1/10 the amount of iron when mixing up the batch) when aiming for pale shades. Some peach and lavender tones that I get have come from a 1/16 dilution of the recipe. So perhaps the amount of iron that you've got on your print is simply overpowering the light amount of dye you're using?
Waiting 24 Hours Between Mixing and Using Your Indigo Vat
Q: I have a question about the 24 hour waiting period from mixing the ingredients to using the vat. Could you tell me a little bit more about that. Is it necessary? I've used the Jacquard (synthetic) product and was able to use immediately after mixing.
A: In a word, yes. The wait is necessary. There is a big difference between the pre-reduced synthetic indigo and the natural indigo contained in the kit. The synthetic ingredients have already been modified to dissolve in water whereas the indigo in my kit does not dissolve in water. The 24 hour period allows the indigo to a) dissolve and b) become properly reduced (able to transfer onto fabric) and also c) the iron and lime in my kit (the activating ingredients) need time to properly combine. If you dye too soon, you'll get very pale blues and run the risk of staining the fabric brown/sludgy with the iron. If you wait the 24 hours, you'll get great color transfer and no staining.
Maintaining Your Whites While Rinsing
Q: I am using an indigo vat but I find in the rinsing process the whites become tainted by the blue. Any suggestions on how to keep the whites white? Also any tips for washing in the machine and maintaining the whites?
A: I have four quick tips for you:
1. Rinse your pieces in fresh water (maybe add a lil dish soap and wash by hand) BEFORE opening (untieing or unclamping).
2. Rinse in COLD water literally AS you open the piece, gradually raising the temperature when the water rinses clear.
3. pH balance the work after first rinse by submerging into water with slight acidity (added vinegar, lemon juice, citric acid powder, black tea, etc).
4. Use washing machine on cold with mild soap the first time around. If it is a top loader, let it fill with water before the dyed goods go in. If it is a top or front loader use the maximum size load setting possible even if you are only washing a couple pieces. The excess rinse water helps keep the background clear.
Quantity of Indigo Paste in a Vat
Q: What quantity of indigo paste do I use to make a vat?
A: I recommend about 15g of the paste per gallon of liquid used to make the vat.
For a 5 gallon ferrous vat I use 60-75g of the paste, 100g iron and 150g lime. After dyeing for a while, I'll usually sharpen with a half dose (50g iron and 75g lime) to stretch out the vat a little bit and do some paler shades of blue.
Pastry Cones for Applying Rice Paste Resist
Q: I'm looking for an alternative to mulberry paper cones for applying rice paste resist to fabrics. Would pastry cones work?
A: Yes, I use pastry cones with a fine tip.
Make sure you pre-screen your dry goods before making your paste to make sure that they can fit through the size tip you’re using. I run my dry ingredients through a 110 mesh screen printing frame. Much of the bran I’ve used in the past has some very large particles that need to be separated or re-milled. I lose about 40% of the bran because the particle size is too large. I use Bob’s Red Mill stabilized rice bran.
Starting Indigo Seeds Indoors Versus Outdoors
Q: I have some indigo seeds and I cannot find any information about starting them outdoors. Do I have to soak and start indoors? I live in northern California and there is no frost and it is nice and sunny. Can I plant them outdoors this week?
A: I'd recommend starting the seeds indoors and keeping a tight eye on the water levels (DO NOT LET THE SEEDLINGS DRY OUT).
I've never directly sown the seeds outdoors but that could work as well, as long as you maintain good moist soil. The overnight soak will definitely help to kick-start things. I've found that pill-bugs LOVE to eat the young leaves so be wary of that and set some traps for them if you can. Over-plant, then you'll want to thin to about 10"-12" on center for your final density of plants.
Here in Los Angeles my plants volunteer from fallen seed of last year's crop. My plants start to grow in December when the rains return and they are almost ready for the first harvest of leaves in May. I think you could get onto a similar cycle up there as long as you never get frost.